Eppeville
About the site
The ENGIE anaerobic digestion plant, located at Eppeville, in the Hauts de France region, covers a 2.5 ha surface and produces 1,815,000 m3 of CH4 per year (18 GWh, gas consumption of 5,000 persons).
Around 230 Nm3 h-1 are injected in continuous into the natural gas grid. Biogas is produced from 30,000 tons y-1 of agro-industrial and agricultural residues.
The plant has a 6,000 m3 digestion volume, with a hydraulic retention time higher than 50 days. The digestate is valorised through land-spreading (6,000 ha, 31 farms).
Our technology in brief
Electromethanogenesis (EMG) is known as a fast-developing process that can produce biomethane directly from CO2 and renewable electricity. The basic principle of this technology is to boost the AD microorganism’s activity by applying a voltage on two electrodes, integrated either directly in the digestate (in-situ), or in a system using biogas as an input (ex-situ). In both cases, the electrodes are covered by electroactive biofilms, capable of exchanging electrons with solid material.
Within the reactor, CO2 reduction into CH4 occurs thanks to the microbial biofilm’s ability to act as a catalyst for these reduction reactions. Protons (H+) and CO2 are thus combined to yield CH4 and water. In an optimally operating plant, no surplus H2 is generated, so the theoretical reaction efficiency is higher than that of electrolysis followed by methanation. Two configurations are possible:
- electrodes in the digester (single chamber), which is then called a bio-electrochemically-improved anaerobic digester (1c-AD-BES).
The electrodes increase the overall biogas production of the AD plant by fostering both oxidative and reductive processes in AD. A 1c-AD-BES will be implemented to produce a biogas with a biomethane content up to 70-80%. - the classic EMG reactor set-up, with two compartments (double chamber) separated by a proton exchange membrane (2c-AD-BES).
Here, water is split on the anode, and CO2 injected at the cathode side is reduced to CH4 on the electrode under the applied voltage. A 2c-AD-BES can be used for the biogas upgrading to high-purity biomethane (>95%) and power-to-gas applications, by bio electrocatalytically converting the remaining biogas CO2 share.
Our ambition
The aim of this innovation is to increase biomethane production on the AD unit using the effluent digestate, biogas of the main digestor and external green electricity from solar and wind. Compared to the sole AD reactor, the goal is to produce up to 43% more biomethane thanks to the combination of both 1c-AD-BES (+20% compared to sole AD reactor) and 2c-AD-BES acting as an upgrading system to reach gas grid quality biomethane up to 95% CH4. The pilot will be composed of two subsystems, both relying on electromethanogenesis with the aim of evaluating their performances.
The expected methane content after the single chamber reactor is 70 – 80%. Further biogas upgrading towards 95% CH4) will be done by the double chamber reactor, installed in series to the single chamber one.
Our challenges
Previous lab experiences showed that two parameters contribute to increase biogas/biomethane production in AD-BES:
- the increased available surface for biofilm growth, due to electrodes presence;
- the application of an optimal voltage for the stimulation of electro-active microorganisms. It is still an open challenge to optimize these two parameters together, to sum their beneficial effects in an upscaled AD-BES plant.
On the other hand, feeding the 1c-AD-BES with an already digested feedstock represents a challenge, as some physical-chemical characteristics are sub-optimal, e.g., basic pH, low carbon/nutrients ratio, low biodegradability, and high viscosity. Moreover, inoculation of anode and cathode with proper electro-active biofilms also represent a challenge, when targeting upscaled, industrial systems. Ideal solution is to cope with both electrodes’ inoculation directly onsite, by direct voltage application (i.e., not using a potentiostat, which is quite common in lab experiments).
Previous work done by LEITAT and ENGIE showed that this approach is possible, but biofilm populations are highly sensitive to applied operation conditions (inoculum mixture, feedstock temperature, voltage). Especially on the cathode site, it is challenging to grow a specific biofilm catalysing CO2 reduction to CH4. For these reasons, the current proposal foresees initial laboratory trials on digestate pre-treatment and electrodes surface treatment solutions for optimized biocatalyst-transducer interface and overpotential minimization (i.e., decrease of electrical energy demand).
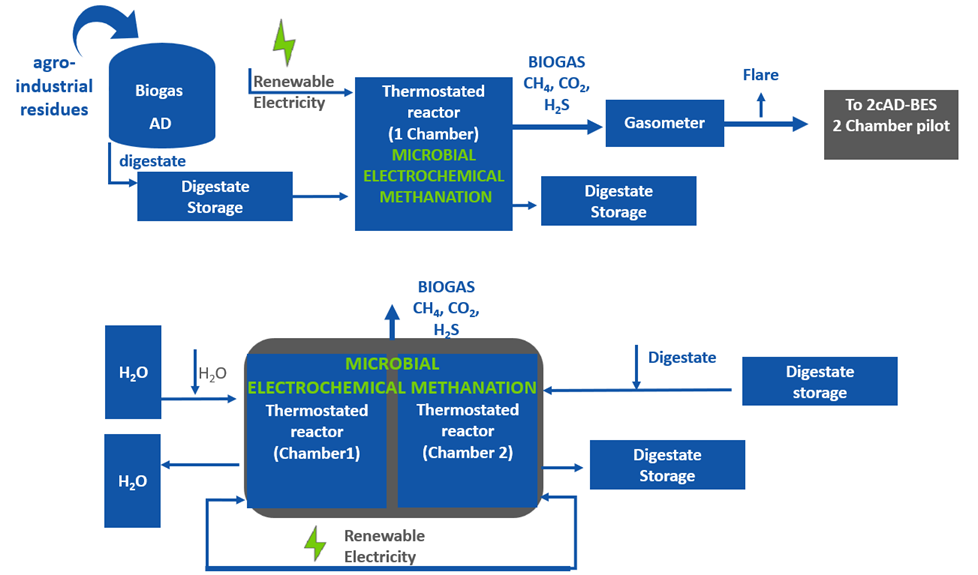