Ladyzhin
About the site
The biogas plant in Ladyzhin, Vinnytsia region, has an installed electric capacity of 12 MW, producing biogas from 330 t d-1 of chicken manure and other agricultural residues, producing 85,000,000 kW of electricity per year.
Plant configuration consists of twelve reactors (9 main reactors and 3 post digestors) with 90,000 m3 volume each.
Also, the complex has its own biogas pipeline that transfers biogas to the cogeneration unit located near the slaughter complex, in order to use heat to supply steam to the latter.
Our technology in brief
During anaerobic digestion, different microorganisms convert organic residues into biogas. The process occurs in four different phases of which the last phase is methanogenesis. Two metabolic pathways of methanogenesis dominate in industrial biogas plants, i.e., acetolactic methanogenesis, where acetate is split into CO2 and CH4 and hydrogenotrophic methanogenesis where CO2 is reduced with hydrogen to CH4. Both processes run in parallel, however the first route will be prevailing if no interventions are made, because the naturally occurring amount of free hydrogen in the substrates is low. By injecting hydrogen directly into an AD reactor, the second route is stimulated and the activity of the hydrogenotrophic methane formers is increased. This results both in an overall increase of the biomethane yield per given amount of feedstock, and in a higher methane concentration in the final biogas produced.
Our ambition
First of all, it is necessary to evaluate different process parameters, e.g., H2 flow rate and methanation rate with respect to process stability and develop process control approaches for in situ methanation. Here, DBFZ will perform several lab tests in the described 50 L reactor setup, amongst others, to examine the process under different controlled conditions and develop process control strategies that will be implemented and validated in the lab reactors of MHP and later transferred to the demonstration reactor.
At the end of the project TRL will be 6-7 due to the demonstration of in-situ methanation in >10 m3 scale at the site of the MHP biogas plant in Ladyzhyn. The demonstrator will be equipped with a gas circulation system like the mixing system in the biogas plants of MHP. H2 is injected into the gas loop of the mixing system, whereas the H2 concentration in the gas phase is monitored and adjusted to levels previously determined under lab conditions. During the demonstration phase, H2 will be provided from a hydrogen tank, once established in full scale an electrolyser for intermittent and power-demand oriented hydrogen production will be used for H2 production.
The overall aim is to increase both the overall methane yield per given amount of feedstock, as well as the methane content of the final biogas produced. The methane concentration in the biogas is foreseen to increase from 55% to 85% by the injection of H2. Hereby the carbon efficiency of the AD process is improved and biomethane production is increased using a comparable technically simple approach that is easy to implement in biogas plants equipped with a gas mixing system.
Our challenges
Important technical and safety aspects need to be considered during in situ methanation. Process parameters, such as concentration of volatile fatty acids and pH, the quality and quantity of biogas, the presence of residual H2 in the biogas, the optimal H2 flow rate, the optimal gas recirculation rate and mixing ratio of hydrogen/raw gas, as well as potential erosion on the existing gas mixing system due to H2 and potential diffusion of hydrogen through the roof membranes of AD reactors will be evaluated in the project.
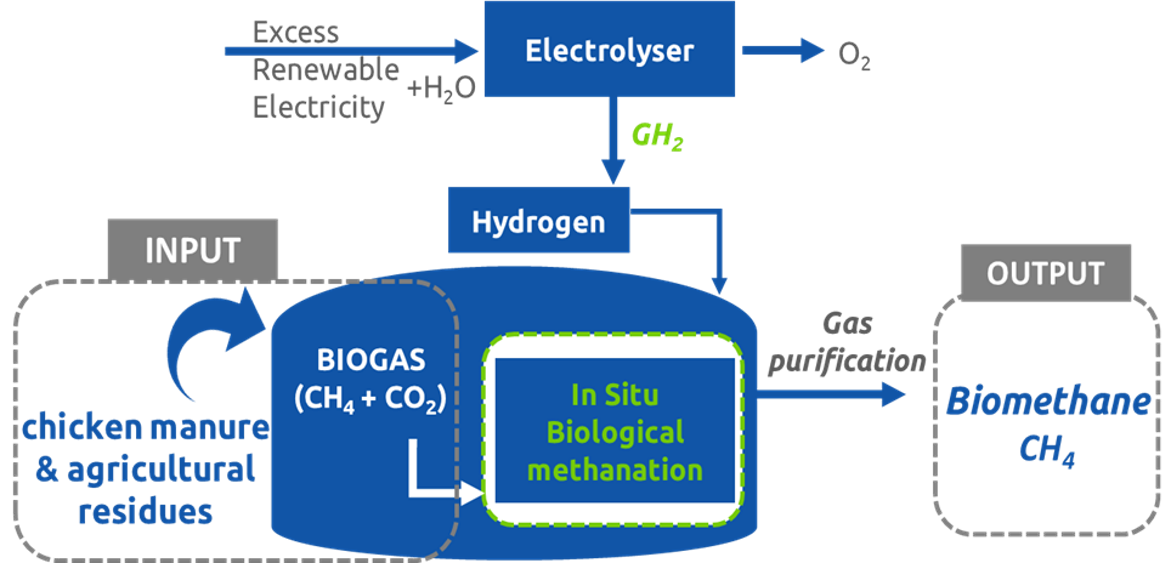